Why is fall protection so important in a warehouse environment?
"Falls are among the most common causes of serious work related injuries and deaths. Employers must set up the work place to prevent employees from falling off of overhead platforms, elevated work stations or into holes in the floor and walls."
- Occupational Safety and Health Administration (OSHA)
Ignoring the importance of fall protection can lead to unsafe working conditions, employee injuries, and costly penalties issued by OSHA and other regulatory agencies. Despite this myriad of unpleasant consequences, many employers do not devote sufficient attention to fall protection.
In fact, fall protection violations ranked number on the list of OSHA's most frequently violated standards with 7,270 violations in 2018. Considering that OSHA recently increased the maximum penalty for single violations to $12,934 and repeat violations to $129,336, your company cannot afford NOT to make fall protection a top priority.
What are the most common warehouse problems that increase slips and falls?
The first step on the path to a sound fall protection plan is to identify problem areas within your warehouse that need attention. This requires a thorough walk through of your facility and a strong working knowledge of OSHA's current fall protection standards. Below are eight of the most common warehouse problems that can lead to slips and falls.
1) Unsecured loading docks
Roughly one out of every four warehouse injuries takes place on a loading dock. The majority of these injuries occur when workers or delivery personnel fall from the loading dock while they are loading and unloading goods. Falls also may result as delivery trucks make a premature departure from the loading dock area.
2) Crowded warehouse aisles
Failure to adhere to safety standards due to excessive inventory or crowded warehouse aisles can put your employees at increased risk for trips and falls. Additionally, your organization could face costly fines for failing to properly manage inventory and keep aisles clear. For instance, one New York company was fined over $160,000 for safety violations that included failure to safely stack merchandise and overcrowded aisles.
3) Poorly designed stairways
"The concept of the handrail is basic. If you slip, trip, or begin to fall while descending a staircase, grabbing the handrail can break your fall and save you from serious injury."
- Auburn University, Risk Management and Safety
Stairways can be extremely hazardous, especially if they are not properly designed or maintained. As you complete your walk through, be sure to carefully inspect your stairways to make sure that they are structurally sound, well-illuminated, and clean. Here are some common problems with stairways that can increase the risk of falls:
- Stairs with loose or missing handrails
- Dark stairwells
- Improperly sized riser height
- Missing or loose stair treads
- Debris or moisture on stairs
- Stairways without doors or signage
4) Unprotected skylights and platform holes
Platform holes, floor holes, and skylights are all fall danger zones for employees. OSHA cautions against the use of double chains as a means of protecting employees from falls at hole entrances. Entrances to ladderways must also be properly secured to protect workers from falls. OSHA suggests a self-closing gate as a proper means of preventing workers from falling.
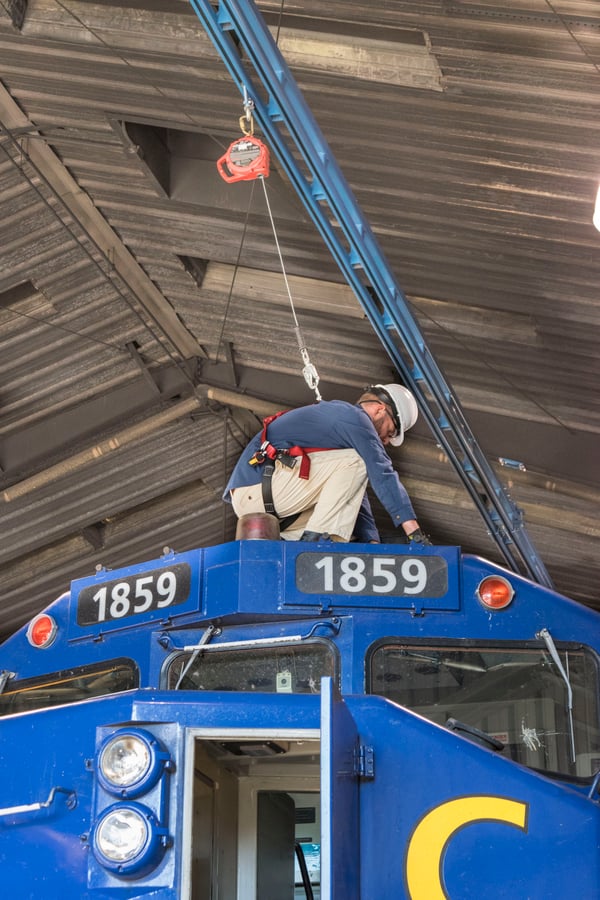
5) Elevation differences without the proper access
Safety managers and engineers are responsible for protecting their employees from falls due to elevation differences. OSHA states that employers "must provide a stairway or ladder at all worker points of access when there is a break in elevation of 19 inches (48 cm) or more and no ramp, runway, embankment or personnel hoist is available." Facilities with elevation differences that lack proper access put employees at increased risk for falls and are subject to penalties.
6) Crowded mezzanines
"Fall-related accidents also are an ever-present danger in elevated work areas such as mezzanines. Additionally, an increasing number of plants and warehouses have pit areas that workers can fall into if they are not guarded properly."
- Andy Olson, EHS Today
Businesses that are bursting at the seams sometimes use mezzanines to store equipment, products, files, and tools. This practice alone will not jeopardize employee safety. However, if mezzanines are overloaded with products and equipment, workers will be more likely to trip and fall from a mezzanine - especially if there are no safety gates or guardrails around the mezzanine.
7) Moisture and spillage on warehouse floors
Workplace falls are not always the result of an employee tripping or plummeting from one level to a lower level. They are sometimes caused when moisture or debris accumulates on the floor. This is especially likely to happen during inclement weather when employees, delivery personnel, and visitors track water and snow indoors.
8) Poorly trained employees
Employees who lack proper safety training create an unsafe work environment for co-workers and visitors. They also put their own lives at risk when they fail to wear the correct personal protective equipment or fail to follow safety procedures.
What steps can you take to address these hazards?
The key to preventing the pitfalls above is to establish a strong culture of safety within your organization. This process starts with the leadership and buy-in of safety managers and plant engineers, who continually emulate the proper safety measures. This includes taking steps to secure loading docks and mezzanines, while also taking a proactive approach to maintaining a clean, dry organized warehouse. Here are five steps you can take decrease the risk of falling within your warehouse:
1) Establish a visual barrier around your loading dock
"For the clear majority of docks, a visual barrier is sufficient. To be as safe as possible, the visual barrier needs to be prominent. The barrier should be a bright color. Yellow is preferred because it's the international safety color indicating "warning." To be productive around busy docks, the visual barrier should be able to be installed and removed as quickly as possible."
- Maree Mulvoy, Safety and Health Magazine
A visual barrier such as a bright yellow guardrail or safety gate can play an instrumental role in preventing falls from loading docks. Additionally, barriers can help truck drivers and forklift operators visualize a loading dock's edge and avoid collisions and other accidents.
2) Invest in a reliable fall protection system
OSHA states that "personal fall arrest systems (PFAS) (such as safety harnesses, lifelines, lanyards) are required" in situations where guardrails are not feasible or in situations that involve work from two-point suspended scaffolding. Positioning device systems may also be used to "provide protection from falling off an unguarded edge" of a platform or mezzanine.
Remember that not all fall protection systems are created equal. When choosing a trusted fall protection partner, be sure to look for a company with decades of experience in creating fall protection equipment. Additionally, make sure that the provider you choose offers the type of system that is best suited for your warehouse. Examples include bridge systems, fold away systems, and swing arm systems.
3) Keep plenty of personal protective equipment (PPE) on hand
"Employers are also responsible for determining whether personal protective equipment (PPE) is necessary, providing it, and ensuring it is being used and maintained properly. Supervisors should also wear gear when appropriate, and stress to workers that wearing isn't just a rule, but that it protects them from injury and illness."
- Sam Puckett, Fulcrum
A lack of access to the proper PPE should never be an excuse for injury or death. Make sure that you have the proper safety harnesses, vests, eyewear, boots, and other industry-specific gear on hand for employees and visitors to access.
4) Post plenty of safety signage
The power of safety signage cannot be overestimated. Warehouse signage serves as a constant visual reminder that workers need to exercise caution and follow safety protocol when performing their jobs. Make sure signs are brightly colored and posted in highly visible areas of your warehouse. Examples include loading dock areas, mezzanines, and stairwells.
5) Keep your warehouse floors clean and dry
"No matter how careful your employees are, if it's snowing outside, they'll track snow into your facility. You may have to increase floor-cleaning intervals in winter. Luckily, there are some great labor-saving devices that make cleanup quick. Broom attachments for forklifts can squeegee water off of floors, and can even push snow piles off the dock for fast and easy maintenance in winter."
- Jennifer Taylor, Solus Group
Keeping your warehouse floors clean and dry is one of the best steps you can take to prevent employees from slipping and falling. You can achieve this goal by keeping a constant stream of air running across your floors. Additionally, make sure you take extra precautions during the winter or during rainy months to help keep moisture at bay.
The Bottom Line
Providing proper fall protection should be a top priority for any safety manager or plant engineer. The process should begin with the identification of your warehouse trouble areas, or problems that could increase fall risks for your employees. Then, by following the five tips above, you can develop a strategy that will help you protect your employees and prevent costly OSHA fines. Click here to learn more about the top fall protection systems available. We invite you to contact us directly at Gorbel. We look forward to serving as your trusted resource for all of your fall protection needs.